Altı Sigma: Kapsamlı Bir Bakış
Altı Sigma , genel olarak süreç iyileştirme ve daha az kusur hedefine sahip bir dizi metodoloji, araç ve tekniktir. Altı Sigma metodolojisi, uygulaması ve daha fazlası hakkında aşağıyı okuyun.
Altı Sigma Nedir?
Altı Sigma’yı tanımlamadan önce, “sigma”nın ne anlama geldiğini anlamak önemlidir. İstatistikte sigma, varyansın karekökü alınarak hesaplanan standart sapma olarak bilinir. Varyans, ortalamadan (ortalama) farkların karelerinin ortalamasıdır.
İmalatta kusurlar, iyi sonuçları kötü sonuçlardan ayıran spesifikasyon sınırları kullanılarak tanımlanır. Altı Sigma süreci, en yakın spesifikasyon sınırından altı standart sapma (sigma) olan bir süreç ortalamasına sahiptir. Altı standart sapma, bir sürecin doğal varyasyonu ile önceden tanımlanmış spesifikasyon limitleri arasında size yeterli bir tampon sağlar. Başka bir deyişle, bir ürünün 10,22 ile 10,28 inç arasında bir kalınlığa sahip olması gerektiğini belirlediyseniz, o zaman işlem ortalaması, 0,005’ten daha az bir standart sapma ile 10,25 civarında olmalıdır (10,28, 10,22’den altı standart sapmadır).
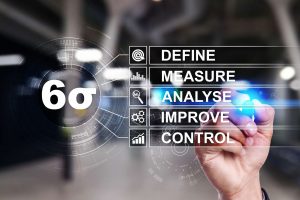
Artık teknik tanımı bildiğimize göre, üretimle ilgili olarak Altı Sigma’ya bakabiliriz. Altı Sigma, genel olarak süreç iyileştirme ve kusurları en aza indirme hedefi olan bir dizi metodoloji, araç ve tekniktir. Daha spesifik olarak, kusurların nedenlerini belirleyerek ve ortadan kaldırarak ve hem üretim hem de iş süreçlerindeki değişkenliği en aza indirerek bir süreçten üretilen ürünlerin kalitesini iyileştirmeyi amaçlar.
Başarılı bir Altı Sigma uygulaması, performansta bir artışa ve süreç varyasyonunda bir azalmaya yol açar, bu da artan karlara, iyileştirilmiş ürün kalitesine ve çalışanların moralinde bir artışa yol açabilir. İstatistiksel olarak, bir parçanın herhangi bir özelliğini üretmek için tüm fırsatların yüzde 99.99966’sının hatasız olması veya milyon fırsat başına 3.4 hata olması beklenmektedir (bu, ortalamada 1.5 sigma kaymayı ifade eder).
Altı Sigma’nın çeşitli tanımlarıyla karşılaşabilirsiniz, ancak hepsi birkaç ortak ideolojiyi paylaşır. Tüm Altı Sigma süreçleri aşağıdakileri içermelidir:
- Şirketin kârlılığını doğrudan etkileyen iyi düşünülmüş ve iyi tasarlanmış projeleri yürütmek için tasarlanmış ekiplerin kullanılması.
- Tüm düzeylerdeki çalışanlara sunulan istatistiksel düşünme eğitimi, seçkin bir azınlığa üst düzey istatistik ve proje yönetimi (kara kuşak olarak bilinir) konularında ileri düzey eğitim sağlar.
- Uygulama için DMAIC yaklaşımını kullanmaya yönelik temel bir metodoloji (aşağıda tartışılmaktadır).
- Üst düzey yönetim, Altı Sigma metodolojilerini bir iş stratejisi olarak benimsemeye isteklidir.
Altı Sigma, bir felsefe ve bir metodoloji olarak ayrılabilir. Felsefesi Altı Sigma yan tanımlandığı ölçülen, analiz edilen, geliştirilmiş ve kontrol edilebilir işlemleri gibi tüm çalışma dikkate alır. Bu süreçler, bir çıktı (y) üreten bir girdiye (x) sahip olmalıdır. Basitçe söylemek gerekirse, girdiyi kontrol ederseniz, çıktıyı da kontrol edebilirsiniz.
Metodoloji Altı Sigma yönü DMAIC yaklaşım olarak canlanır -, ölçü, analiz iyileştirmek ve kontrol etmek tanımlamak. Esasen DMAIC, sorunu tanımlamakla başlayıp uzun vadeli bir çözümü uygulamaya koymakla biten her ekibin izlemesi gereken yol haritasını ortaya koyuyor. Aşağıda DMAIC’i daha ayrıntılı olarak tartışacağız.
Altı Sigma, istatistiksel süreç kontrolü (SPC), süreç haritalama, FMEA ve daha fazlası gibi hem nicel hem de nitel yalın üretim araçlarını kullanır .
Sigma Seviyeleri | ||||
---|---|---|---|---|
Sigma Düzeyleri (Z) | Milyon Fırsat Başına Hata (DPMO) |
Yüzde Kusur (%) |
Yüzde Başarı (Verim %) |
Yetenek (CP) |
1 | 691.462 | 69 | 31 | 0.33 |
2 | 308.538 | 31 | 69 | 0.67 |
3 | 66.807 | 6.7 | 93.3 | 1.00 |
4 | 6.210 | 0.62 | 99.38 | 1.33 |
5 | 233 | 0.023 | 99.977 | 1.67 |
6 | 3.4 | 0.00034 | 99.99966 | 2.00 |
Altı Sigma: Bir Analoji
Altı Sigma’yı ve bunun değişkenlerle ilişkisini anlamak için en iyi benzetmelerden biri, bir arabayı garaja park etmek. Arabanız garajdan daha genişse, giremezsiniz. Ardından, garajın genişliğinden biraz daha az genişliğe sahip bir araba alın. Dikkatli bir yaklaşımla, araba garaja park edilebilir, ancak muhtemelen dikkatsizlik nedeniyle zamanla çizilecektir. Son olarak, garajın genişliğinin yarısı kadar genişliğe sahip bir araba hayal edin. Artık herkes arabasını garaja park edebilir, çift vardiyadan gelen ve gözlerini zar zor açık tutanlar bile.
Bu benzetmede araç genişliği, kuruluşunuzun mevcut süreçlerini ve yeteneklerini temsil eder. Garajın genişliği, müşterinizin özelliklerini temsil eder. Altı Sigma’nın ilkelerine, onu nasıl uygulayabileceğinize ve diğer şirketlere nasıl yardımcı olduğuna daha yakından bakalım.
Altı Sigma’nın 5 İlkesi
Altı Sigma’nın beş ilkesi, Altı Sigma ile harmanlanmış yalın üretim ilkelerinin bir şekilde doruk noktasıdır. Yalın üretim, sekiz tür israfın azaltılmasını veya ortadan kaldırılmasını vurgular. Altı Sigma, istatistiksel analiz kullanarak ürün çeşitliliğini ve kusurlarını azaltmayı amaçlar. Bunlar birlikte uygulandığında Altı Sigma’nın beş ilkesini elde edersiniz.
-
- Müşteriye odaklanın: İşiniz ne olursa olsun, her zaman müşterilerinizi ilk sıraya koymaya çalışmalısınız. Süreçlerinizde büyük veya küçük herhangi bir değişiklik yapmadan önce, “Bu, müşterilerimizi nasıl etkileyecek?” sorusunu sormanız önemlidir. Sizin ve ekibinizin aldığı herhangi bir karar, sizi müşterinize maksimum değeri sağlamaya yaklaştırmalıdır.
-
- Sorunu bulun: Bu adım, mevcut değer akışınızdaki sorunların temel nedenini bulmaya odaklanır. Altı Sigma, yalnızca geri adım attığınızda ve süreçlerinizin mevcut durumuna ve belirlenen atık alanlarına bir göz attığınızda çalışır. Örneğin herhangi bir montaj hattı sürecini ele alalım. Bir avuç plastik, cam ve bilgisayar çipi nasıl iPad olur? Parçaların satın alınmasından başlayarak montajına ve nihai ürünün dağıtımına kadar her adımı değerlendirin. Bu kapsamlı inceleme, değer katan ve katmayan adımları belirlemenize olanak tanır.
-
- Atıklardan kurtulun: Değer akışınızı inceledikten ve atık alanlarını belirledikten sonra, artık çöpü çıkarmanın zamanı geldi. İş akışınızdaki tüm sorunları – değersiz süreçler veya kusur fırsatları – ortadan kaldırın. Değer akış haritanız israf alanlarını veya sorunların nerede olduğunu kolayca ortaya çıkarmıyorsa, daha derine inmek için yalın araçları kullanabilirsiniz. Atıkları tanımlamaya yönelik popüler bir araç, kılçık diyagramıdır ( burada ele alınmıştır ).
- Süreci harekete geçirin: Ardından, yeni ve geliştirilmiş süreçleri çalıştırın. Bunu, her çalışana yeni standartlar, prosedürler veya uygulamalar hakkında eğitim vererek yapın. Tüm personel, değişikliklerin günlük süreçlerini doğrudan nasıl etkilediğini ve bunların şimdi nasıl değişeceğini bilmelidir.
- Bir değişim ve esneklik kültürü yaratın Altı Sigma metodolojisinin uygulanması için yapılan tüm çalışmalar, organizasyonun her seviyesi değişmeye istekli değilse reddedilir. Çalışanları değişimi kabul etmeye teşvik edin ve değişimle birlikte gelen korkuları gidermeye yardımcı olun. Altı Sigma ile ilgili korku, genellikle çalışanlar tarafından normal olarak gerçekleştirilen süreçlerin ortadan kaldırılmasından veya otomasyonundan kaynaklanır.
Altı Sigma’yı Uygulamak: DMAIC ve DMADV
Altı Sigma, iki metodolojiden biri kullanılarak uygulanır: DMAIC veya DMADV. Bir kuruluş mevcut süreçlerini iyileştirmek istediğinde DMAIC (tanımla, ölç, analiz et, iyileştir ve kontrol et) kullanılır. DMADV (tanımla, ölç, analiz et, tasarla ve doğrula) bir kuruluş yeni süreçler yaratırken kullanılır. İki metodoloji birkaç yönden benzerdir. İkisi de alışık:
- Hata sayısını azaltın
- Verileri ve istatistiksel araçları kullanarak belirlenen sorunlara kaliteli çözümler bulun
- Kuruluşların finansal ve ticari hedeflerine ulaşmasına yardımcı olun
İki metodolojinin birbirinden nasıl farklılaştığına dair bir anlık görüntüye bakalım.
- DMAIC: DMAIC kullanan kuruluşlar, çözmek istedikleri sorunu/sorunları özetleyerek tanımlama aşamasıyla başlar. Ardından ekip, mevcut süreçleri ölçer ve haritasını çıkarır, veri toplar ve herhangi bir sorunun temel nedenini belirler. Analiz aşaması, ekibin mevcut sürecin atıklarını ve kusurlarını doğrulamak için çalışırken verileri analiz ettiği aşamayı takip eder. Analiz tamamlandıktan sonra ekip, israfı ve kusurları en aza indirmeye yönelik yeni ve geliştirilmiş süreçleri uygulamaya çalışır. Son adım, ekibin her çalışanın uygulayacağı yeni süreçleri belgelediği ve düzenlediği kontrol aşamasıdır.DMAIC aşağıdakilere odaklanır:
- Kuruluşunuzun iş süreçlerini tanımlama
- Mevcut süreçlerin performansının ölçülmesi
- Sorunların temel nedenini bulma
- Mevcut süreçleri iyileştirerek kusurları azaltmak
- İşlemler artık çalışmadığında uyarmak için kontroller uygulamak
- DMADV: Yeni süreçler yaratması gereken kuruluşlar, müşteri ihtiyaçlarını en baştan karşılamak amacıyla DMADV metodolojisi ile başlamalıdır. Tasarım aşamasında ekip, nihai hedefleri ve çıktıları ölçmelidir. Ardından, istenen çıktıları gerçekleştirmek için hayati önem taşıyan faktörleri değerlendirin. Bu faktörler ölçüldüğünde, ekip istenen sonucu elde etmek için mümkün olan en iyi seçenekleri analiz edebilir. Artık ekip üyeleri, müşterinin çıktılarını karşılaması gereken süreçleri tasarlamaya hazır. Son olarak, hedeflere ulaşıldığından emin olmak için herkes nihai sonuçları doğrulamalıdır. DMADV aşağıdakilere odaklanır:
- Müşteri ihtiyaçlarının tanımlanması ve ölçülmesi
- Müşteri ihtiyaçlarını karşılayacak süreç seçeneklerinin baştan belirlenmesi
- Müşterinin ihtiyaçlarına odaklanan bir iş modeli tasarlamak
- İş modelinin müşterinin ihtiyaçlarını karşıladığını doğrulamak
Altı Sigma Seviyesi ve Dövüş Sanatları Yapısı
Altı Sigma programının başarısı nihayetinde bir bütün olarak ekibe bağlıdır. Altı Sigma’yı uygun şekilde uygulamak, özellikle bir takıma liderlik edecekseniz, önemli miktarda eğitim gerektirir. Ekip liderlerinin Altı Sigma profesyonel sertifikası almaları iyi bir fikir olsa da, ekip üyelerinin süreç hakkında temel bilgi ve anlayış kazanmaları için en azından bir düzeyde sertifikaya sahip olmaları yardımcı olur. Altı Sigma, dövüş sanatlarında bulunanlara benzer şekilde beceri seviyesini, deneyimi ve bilgiyi belirtmek için kemer seviyelerini kullanır.
-
- Beyaz kuşak: Altı Sigma’nın başlangıç kuşağı olan beyaz kuşak sertifikası, Altı Sigma metodolojisini ve bunun organizasyonlarını nasıl etkileyebileceğini öğrenmeye başlamak isteyen profesyoneller içindir. Beyaz kuşaklar, fabrika katındaki işçilerden C düzeyindeki yöneticilere kadar çeşitlilik gösterir ve genellikle birkaç saatlik eğitim gerektirir. Onaylandıktan sonra beyaz kuşaklar, ekiplere problem çözme ve Altı Sigma işyeri kültürünü uygulama konusunda liderlik etmede yardımcı olabilir.
-
- Sarı kuşak: Sarı kuşak sertifikası, beyaz kuşaktan öğrenilen temel bilgilere dayanmaktadır. Sarı kuşaklar, Altı Sigma ile sıkça kullanılan araçlara ve jargonlara aşina olur ve genellikle 10 ila 15 saatlik eğitimden geçer. Sarı kuşaklar, yeşil veya siyah kuşak sertifikalı eğitmenler altında çalışır ve süreç haritaları oluşturmak ve veri toplamakla görevlidir. Her seviyedeki çalışan için beyaz ve sarı kuşak eğitimi önerilir.
-
- Yeşil kuşak: Yeşil kuşaklar, herhangi bir Altı Sigma ekibinin kalbidir; Altı Sigma proje ekibinin iş çıktılarının çoğu yeşil kuşaklar tarafından yapılır. Yeşil kuşaklar genellikle zamanlarının yüzde 25 ila 50’sini Altı Sigma projelerine ayırır ve Altı Sigma metodolojileri, felsefeleri ve ilkeleri konusunda uzman olarak kabul edilir. Sertifika gereksinimleri işverene bağlı olarak değişebilir, ancak yeşil kuşakların genellikle sertifika almadan önce belirli sayıda ders saati tamamlaması, yazılı bir testi geçmesi ve bir Altı Sigma projesine katılması gerekir.Yeşil kuşaklar normalde, veri toplama ve analiz etme yoluyla, atıkların belirlenmesi ve kuruluş genelinde iyileştirmelerin uygulanması sürecine öncülük eder. Yeşil kuşaklar, güçlü analitik ve iletişim becerilerine sahip olmalıdır ve tipik olarak orta ila üst düzey yönetim rolünde çalışanlardır.
- Kara kuşak: Siyah kuşaklar tam zamanlı Altı Sigma uygular ve yeşil, sarı ve beyaz kuşaklardan oluşan birden çok takımı yönetmekle görevlendirilir. Önceki üç sertifika düzeyine ek olarak, kara kuşaklar yazılı bir testi geçmeli ve iki Altı Sigma projesini tamamlamalıdır. Sertifikalandırıldıktan sonra, kara kuşaklar süreç iyileştirme ve istatistiksel analiz tekniklerinde uzmanlaşacak, insanlarla başa çıkmak için üst düzey bir yetenek geliştirecek ve birden fazla ekip için akıl hocası ve lider olarak hareket edecek. Kara kuşaklar ayrıca gerektiğinde ekip liderlerine Altı Sigma ilkelerini öğretebilmelidir.
- Ana kara kuşak: Altı Sigma sertifikasının son seviyesi, ana kara kuşaktır. Bu, bir çalışanın kapsamlı eğitim ve testleri tamamladığını, Altı Sigma kavramlarına hakim olduğunu ve ekipleri disiplinli ve odaklı bir şekilde yönettiğini gösterir. Bu seviye, beş yıl siyah kuşak olarak çalıştıktan veya 10 Altı Sigma projesini tamamladıktan sonra gerçekleştirilir. Siyah ve yeşil kuşaklara öğretmen ve danışman olarak hizmet etmenin yanı sıra, usta kara kuşaklar, üst düzey yöneticilerle iletişim kurmak ve potansiyel Altı Sigma projelerini sağlamlaştırmakla görevlendirilir. Usta kara kuşaklar normalde herhangi bir takımın tam zamanlı üyesi olarak hareket etmezler. Genellikle birden fazla ekip için engellerin üstesinden gelmelerine ve ortaya çıkabilecek soruları yanıtlamalarına yardımcı olmak için akıl hocası veya danışman rolünü üstlenirler.
Altı Sigma Vaka Çalışmaları
Altı Sigma’yı uygulamanın iç işleyişi hakkında okumak ve kuruluşunuzdaki israfı ortadan kaldırmaya ve kusurları en aza indirmeye nasıl yardımcı olabileceğini hayal etmek bir şeydir, ancak bazı tanınmış markalara nasıl yardımcı olduğuna dair en ünlü örneklere bir göz atalım. .
Ford Motor Co.
Ford, 2001 yılında Altı Sigma’yı uygulamaya başlayarak, Altı Sigma’yı büyük ölçekte uygulamaya koyan dünyanın ilk otomobil üreticisi oldu. Ford, dört faktörü iyileştirmeye dayalı bir Altı Sigma girişimi uygulamak istedi: maliyet, kalite, müşteri memnuniyet oranları ve çevresel etki.
- Maliyet azaltma: Ford’un üretim süreci, kesinlikle gerekli olmayan kaynakların kullanılması nedeniyle maliyetliydi.
- Kalite iyileştirme: Ford, kabul edilebilir bir rakam olmasına rağmen, yaklaşık 19.000 kusur örneğine izin veren yüzde 99’luk bir kalite seviyesine sahipti. Altı Sigma’nın yüzde 99.99967 kalite seviyesini benimseme hedefiyle, milyon başına kusur sayısı yaklaşık yedi ile sınırlandırılarak Ford için önemli kalite iyileştirmeleri sağlanıyor.
- Düşük müşteri memnuniyeti derecelendirmeleri: Müşteri memnuniyeti neredeyse her zaman ürün kalitesinden kaynaklanır. Ford, kaliteyi artırmak için Altı Sigma’yı uygulayarak süreçleri düzene sokarak ve üretim sorunlarını iyileştirerek müşteri memnuniyeti oranlarının üstesinden geldi.
- Çevresel etkiyi azaltmak: Tasarım gereği Altı Sigma yeşil bir felsefedir. Ford, Altı Sigma aracılığıyla, yaşamsal kaynakların tüketimiyle ilişkili maliyetleri azaltarak yeşil bir çalışma kültürüne kendini adamıştır.
Ford liderliğini eğittiğinde, yaklaşık 12.500 kişi yeşil, siyah ve ana kara kuşak olarak sertifikalandırıldı ve bunlardan 3.125’ü siyah kuşak sertifikasına sahipti. Ford’un hedefi, üretilen her 18.3 araç için kusur sayısını bire indirmekti. Eğitim lisanslarına 8 milyon dolarlık yatırımın yanı sıra eğitim, yeni ekipman ve yazılım için binlerce saat yatırım yaptıktan sonra şirket hedefine ulaştı. Bu değişiklik diğer süreçlerde dalgalandı ve tesadüfen yukarıda bahsedilen dört faktörü iyileştirdi.
Altı Sigma, yalnızca 2003 yılında Ford’un kârına 61 milyon dolar katkıda bulundu. Sonuç olarak şirket, veriye dayalı süreç iyileştirme gibi Altı Sigma tekniklerini uyguladığından bugüne kadar 3,45 milyar dolardan fazla atığı ortadan kaldırdı ve bugüne kadar yaklaşık 14.200 iyileştirme projesini tamamladı. Ford, müşteri memnuniyeti notunu da altı puan artırdı.
Ford’un Altı Sigma başarısı, yol boyunca bazı hıçkırıklar olmadan değildi. Şirket, başarılı bir Altı Sigma programını uygulamak için üzerinde çalışılması gereken birkaç engelle karşılaştı. Ford, her düzeyde çalışan bağlılığıyla ilgili sorunlar yaşadı. Şüphecilik, otomobil üreticisinin yaklaşık 350 üst düzey yöneticisini ve liderini haftalarca eğitimden geçirmesini de zorlaştırdı. Ford, bağlılık eksikliğinin yanı sıra, çalışanların eğitimi söz konusu olduğunda zaman ve para sorunlarıyla da karşı karşıya kaldı.
Son olarak, Ford, Altı Sigma girişimini uygulamak için gereken veri miktarını yönetecek donanıma sahip değildi. Mevcut değer akışının düzgün bir resmi için yeterli veri toplamak için yeni ölçüm sistemleri oluşturmak ve uygulamak zorunda kaldı. Bu sorunlar üzerinde çalışmak, şirketteki herkesin tam bir taahhütte bulunmasını gerektiriyordu. Tüm personel gemiye bindikten sonra, kaçınılmaz olarak önemli sonuçlar geldi.
Starbucks
Starbucks’ın Seattle’daki tek bir kahve dükkanından 120 ülkede 33.000’den fazla mağazaya gitmesi sadece 37 yıl sürdü. Bu hızlı büyüme, kahve devini sakin, dinlendirici bir kahvehane atmosferinden daha çok fast food tarzı bir işletmeye geçmeye zorladı. Şirket büyümeye devam ederken, müşterileri onu artık bilinen iki uygulamayı benimsemeye zorladı: hız ve doğruluk. İnsanlar kahvelerinin dakikalar içinde taze ve hazır olmasını istiyor.
Starbucks yönetimi, bir anne baba kahvehanesinin insan unsurundan ve kişisel dokunuşundan ödün vermeden bir fast-food restoranının hızını sunmanın bir yolunu bulmaya çalıştı. Altı Sigma eğitiminden geçtikten sonra şirket yönetimi, insanların kahve sipariş etme şeklini ve mağaza içi deneyimlerini dönüştüren iki süreç değişikliği ile geldi.
Starbucks, ilk değişikliği gerçekleştirmek için baristalarına yeni eğitimler verdi. Müşteriler ödeme yapmak için kasaya geldikçe daha proaktif bir rol üstlenen baristalar, siparişleri müşteri ödemeden önce aldı. Bu, bekleme sürelerini önemli ölçüde hızlandırdı. Ek olarak Starbucks, müşterilerin mağazaya gelmeden önce içecekleri önceden sipariş etmelerine ve ödeme yapmalarına olanak tanıyan bir mobil uygulama geliştirdi. Hazır içecekler daha sonra isme göre düzenlenir ve müşteriler geldiğinde barda bekler.
Yönetim, insan unsurunu akılda tutarak, baristaları müşterilerle ilişki kurmaya ve her işlemi kişisel hale getirmeye teşvik etti. Son olarak, mobil uygulamayı düzenli olarak kullanan müşteriler için Starbucks bir ödül programı uyguladı.